the designer's dilemma.
developing bolt torque specifications for safe and reliable joints
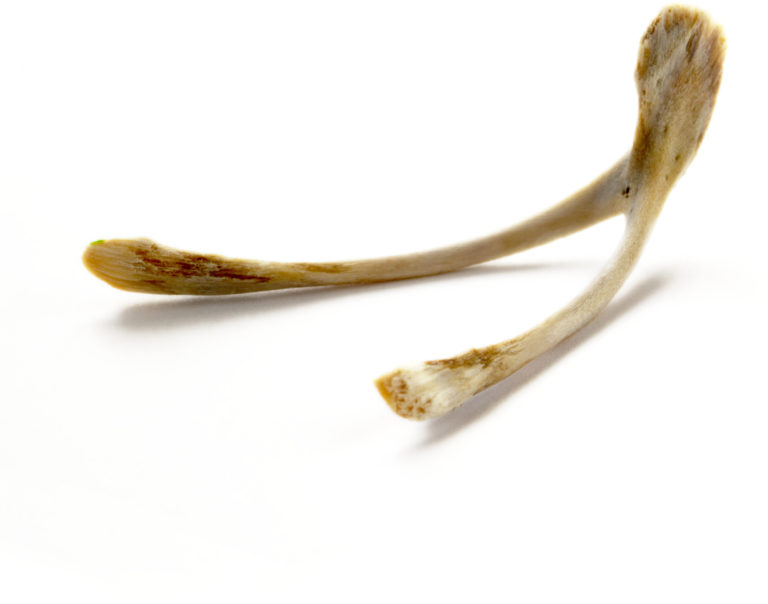
Everybody understands the importance of proper bolt "tightness"; Joints can fail if the fasteners are either too loose or if they're too tight. Therefore, it is imperative that the joint's designer calculates the correct "sweet spot". Valid empirical engineering principals are used in the determination of this vital bolt stress. However, when it comes to specifying the bolt torque, the engineer's careful and disciplined approach must be thrown out the window and immediately replaced by shady engineering voo-doo. Strong words indeed but how else can the institutionalised practice of predicting the future be described?
When a nut or bolt head is rotated across a surface and when threads engage their mates, resistance to further turning develops. These factors of friction are applied to the bolt torque formula. Alas, they're problematic: If more resistance is encountered during future assembly than the designer had predicted, even the most careful adherence to the torque spec would mean that the tightened bolts would be too loose. But on the other hand, if the actual friction is less than the designer had assumed, the bolts would be over-tightened at the same specified torque. The crux is that myriad factors affect friction which cannot possibly be foreseen when the torque specification is initially defined. Yet, in order to ensure that the joint will be reliable and that each fastener will apply the necessary clamp load regardless of what the actual variables will be at any time in the future, the designer's prediction of all possible singular levels of friction must be correct!
So what is a designer to do? How can the potentially-dangerous condition of either under-tightened or over-tightened fasteners be avoided? How can the engineer ensure that the correct friction factor is used in the calculation of the bolt torque specification? In the absence of specifying a logical bolt-stress verification approach for critical applications, the following is a typical workflow:
- arrange "special" candles into a circle on the office floor
- light those candles
- reach into the desk for the magic chicken bones
- draw the curtains closed
- chant
- throw the bones into the burning circle (being careful not to singe them)
- continue chanting
- ask the Magic Spirits for divine guidance by stating how much friction bolt number 1 will experience during tightening intervention number 1
- record the quoted factor
- repeat the above for the next bolt and continue doing this until the friction factors have been predicted for all bolts within the flange
- repeat the process for every subsequent intervention (the next times that the joint will be opened and closed again)
- record all of the resultant factors onto individual Post-it notes
- open the curtains, douse the candles, put the chicken bones away
- collect the notes and tape them onto the Enchanted Dart Board
- reach into the desk for the Mystical Dart
- throw the dart at the board (hopefully hitting one of the notes)
- read the number written on the impaled note
- use that factor in the torque calculation and hope that the joint is so over-designed that accurate bolt tightness (bolt stress) is not important. If this isn't the case...
- referring to each Post-it note, develop unique torque specifications for every individual bolt at initial assembly and also at each future reassembly
- print the massive tome of torque specifications and quickly send it to the boss for review using the fastest unicorn in the corral
On-site Verification. Our speciality.